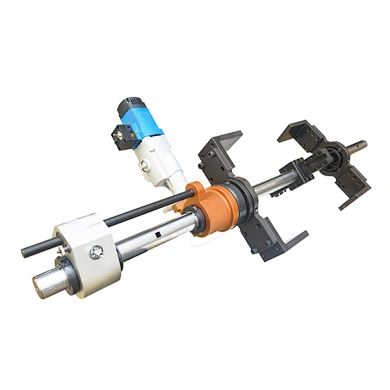
# Flange Facing Machine: Essential Equipment for Precision Machining
## Introduction to Flange Facing Machines
Flange facing machines are specialized tools designed for machining and resurfacing flanges in various industrial applications. These machines play a crucial role in maintaining the integrity of piping systems by ensuring proper sealing surfaces on flanges. Whether in petrochemical plants, power generation facilities, or shipbuilding industries, flange facing machines provide efficient solutions for on-site machining operations.
## Key Features of Modern Flange Facing Machines
Modern flange facing machines incorporate several advanced features that enhance their performance:
– Portable design for on-site operations
Keyword: Flange facing machine
– High-precision machining capabilities
– Adjustable cutting parameters
– Compatibility with various flange sizes
– Durable construction for industrial environments
## Applications Across Industries
Flange facing machines serve critical functions in multiple sectors:
### Oil and Gas Industry
In refineries and pipelines, these machines ensure proper sealing of flange connections, preventing leaks in high-pressure systems.
### Power Generation
Power plants rely on flange facing machines to maintain turbine connections and steam piping systems.
### Marine Engineering
Shipbuilders use these machines to maintain flange surfaces in propulsion systems and piping networks.
## Benefits of Using Flange Facing Machines
The advantages of incorporating flange facing machines into maintenance operations include:
– Reduced downtime by enabling on-site repairs
– Cost savings compared to flange replacement
– Improved safety through proper sealing surfaces
– Extended equipment lifespan
– Consistent machining quality
## Choosing the Right Flange Facing Machine
When selecting a flange facing machine, consider these factors:
– Maximum flange diameter capacity
– Power requirements
– Portability needs
– Material compatibility
– Available accessories and tooling options
## Maintenance and Safety Considerations
Proper maintenance ensures optimal performance and longevity of flange facing machines:
– Regular lubrication of moving parts
– Inspection of cutting tools
– Proper storage when not in use
– Operator training for safe operation
– Compliance with manufacturer’s maintenance schedule
## Future Trends in Flange Facing Technology
The industry continues to evolve with new developments:
– Integration of digital controls and automation
– Improved materials for longer tool life
– Enhanced portability features
– Smart monitoring systems for predictive maintenance
– Environmentally friendly machining solutions
Flange facing machines remain indispensable tools for industries requiring precision machining of flange surfaces. As technology advances, these machines continue to offer more efficient, precise, and user-friendly solutions for maintaining critical piping connections across various sectors.