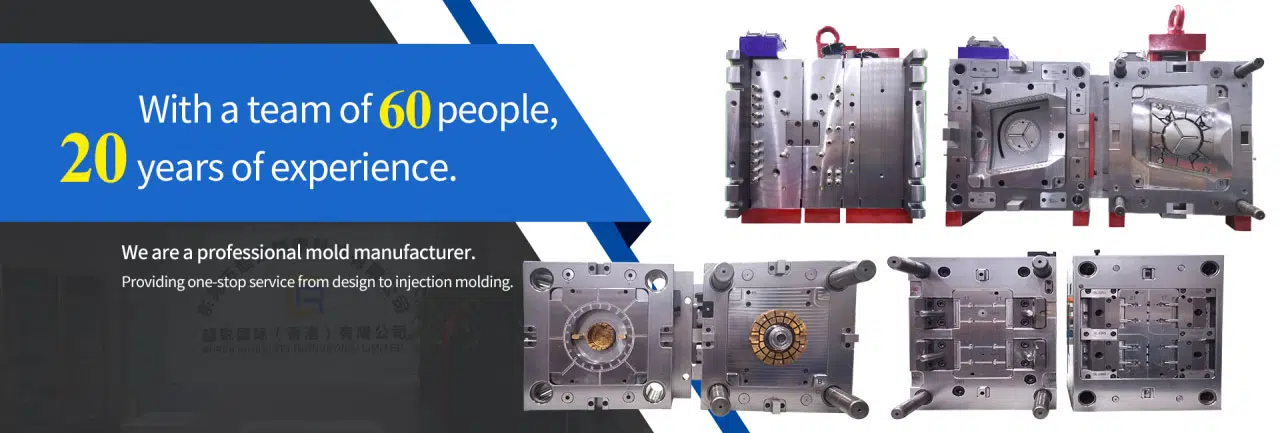
# Sand Casting Process Overview
## Introduction to Sand Casting
Sand casting is one of the oldest and most widely used metal casting processes. This versatile method involves pouring molten metal into a sand mold cavity, where it solidifies to form the desired shape. The simplicity and cost-effectiveness of sand casting make it a popular choice for producing both small and large metal parts across various industries.
## The Basic Steps of Sand Casting
### 1. Pattern Creation
The process begins with creating a pattern, which is a replica of the final product. Patterns are typically made from wood, plastic, or metal and include allowances for shrinkage and machining.
### 2. Mold Preparation
A mixture of sand and binder is packed around the pattern to create the mold. The mold consists of two halves:
– The cope (top half)
– The drag (bottom half)
### 3. Core Making (if needed)
For parts with internal cavities, sand cores are created separately and placed in the mold before pouring.
### 4. Pouring the Molten Metal
The molten metal is poured into the mold through a gating system, which includes:
– Pouring cup
– Sprue
– Runners
– Gates
### 5. Cooling and Solidification
The metal is allowed to cool and solidify within the mold. Cooling time depends on the metal type and part thickness.
### 6. Shakeout and Cleaning
After solidification, the sand mold is broken away, and the casting is removed. Excess material (gates, risers) is removed, and the casting is cleaned.
## Advantages of Sand Casting
– Cost-effective for low to medium production quantities
– Can produce very large parts (up to several tons)
– Works with nearly all metal alloys
– Allows for complex geometries
– Quick tooling turnaround compared to other casting methods
## Common Applications
Sand casting is used in numerous industries, including:
– Automotive (engine blocks, cylinder heads)
Keyword: Sand Casting
– Aerospace (turbine housings)
– Construction (pipes, fittings)
– Agriculture (equipment parts)
– Art and sculpture
## Variations of Sand Casting
Several specialized sand casting methods exist:
– Green sand casting (most common)
– Resin sand casting
– Shell molding
– Vacuum molding
## Conclusion
Sand casting remains a fundamental manufacturing process due to its flexibility, cost-effectiveness, and ability to produce complex metal parts. While newer casting technologies have emerged, sand casting continues to be the preferred choice for many applications where these advantages outweigh the need for extremely tight tolerances or smooth surface finishes.