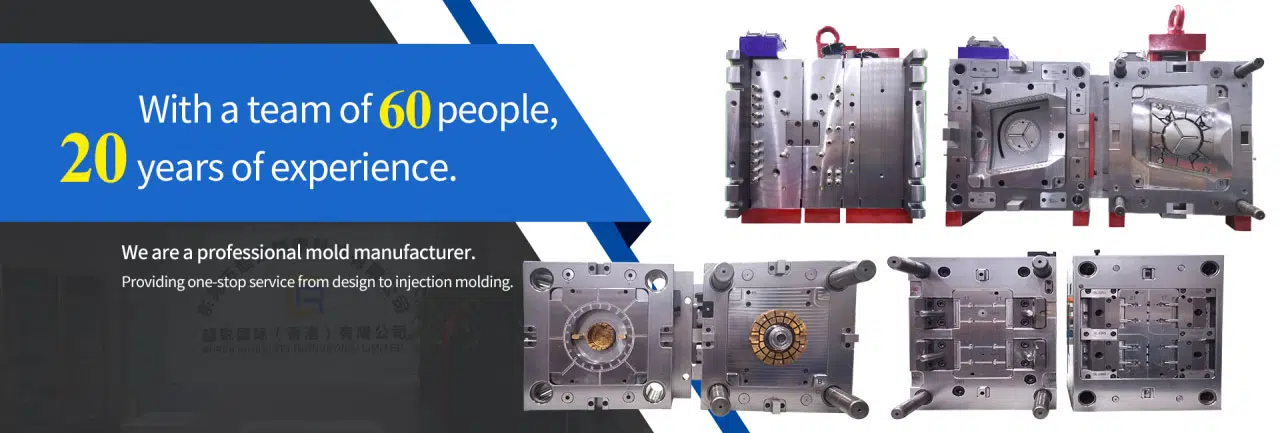
# Export Mold Production: A Comprehensive Guide
## Understanding Export Mold Production
Export mold production refers to the process of designing, manufacturing, and shipping molds to international markets. This specialized manufacturing sector plays a crucial role in global supply chains, particularly for industries requiring precision components such as automotive, electronics, and consumer goods.
The mold export industry has grown significantly in recent years, with manufacturers seeking cost-effective solutions without compromising on quality. Countries with strong manufacturing bases have become hubs for export mold production, offering competitive pricing and technical expertise.
Keyword: Export Mold Production
## Key Considerations in Export Mold Production
When engaging in export mold production, several critical factors must be considered:
1. **Material Selection**: Choosing the right steel or aluminum alloy based on the production volume and part requirements
2. **Precision Engineering**: Ensuring tight tolerances that meet international standards
3. **Surface Finish**: Achieving the required surface quality for the final product
4. **Production Capacity**: Matching the mold design with the intended production output
5. **Shipping Logistics**: Planning for safe transportation of delicate molds
## The Export Mold Production Process
The typical workflow for export mold production involves several stages:
### 1. Design and Engineering
This initial phase includes 3D modeling, flow analysis, and structural simulations to create an optimal mold design. Engineers consider factors like cooling channels, ejection systems, and gate locations to ensure efficient production.
### 2. Material Procurement
High-quality steel or aluminum is sourced based on the project specifications. Common materials include P20, H13, and S136 steels for their durability and performance characteristics.
### 3. CNC Machining
Advanced CNC machines create the precise cavities and cores of the mold. This stage requires skilled operators and quality control measures to maintain dimensional accuracy.
### 4. Assembly and Testing
Components are assembled, and trial runs are conducted to verify performance. Adjustments are made as needed before final approval for shipment.
### 5. Packaging and Shipping
Specialized packaging protects molds during transit. Proper documentation ensures smooth customs clearance in the destination country.
## Quality Standards in Export Mold Production
International buyers expect molds to meet rigorous quality standards:
– ISO 9001 certification for quality management systems
– Compliance with industry-specific standards (automotive, medical, etc.)
– Detailed inspection reports including dimensional checks and material certifications
– Proper documentation for traceability and maintenance purposes
## Choosing the Right Export Mold Manufacturer
When selecting a partner for export mold production, consider:
– Years of experience in international mold exports
– Portfolio of successful projects in your industry
– Technical capabilities and equipment inventory
– Communication skills and language proficiency
– After-sales support and warranty policies
## Future Trends in Export Mold Production
The industry continues to evolve with several emerging trends:
– Increased automation in mold manufacturing processes
– Growing demand for sustainable materials and processes
– Adoption of Industry 4.0 technologies for smarter production
– Expansion of additive manufacturing for mold components
– Greater emphasis on rapid prototyping capabilities
Export mold production remains a vital service for manufacturers worldwide, enabling cost-effective production of high-quality plastic and metal components across borders.